A relatively simple layout
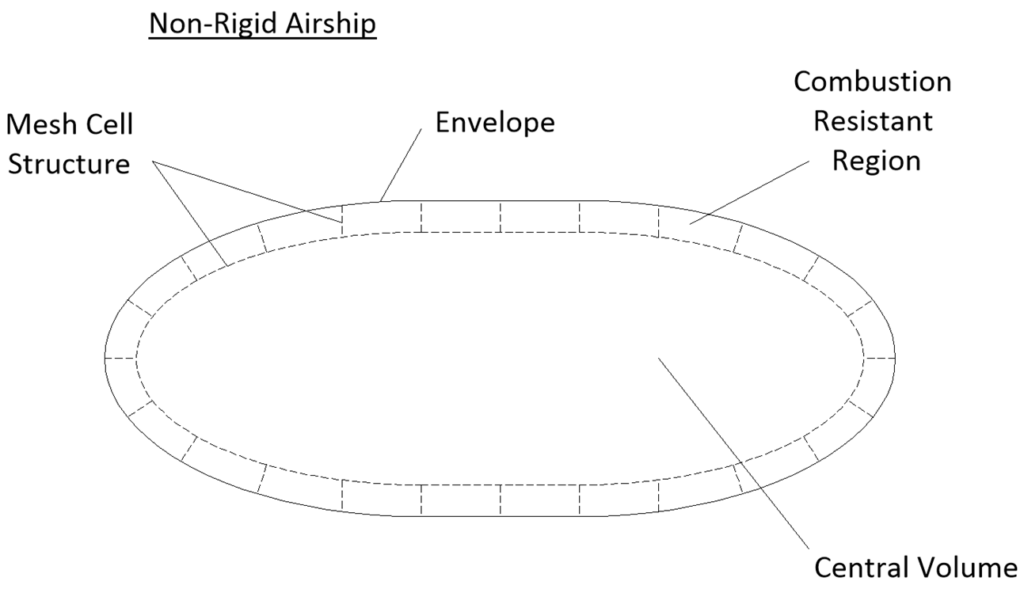
A non-rigid airship comprises an envelope which contains the lifting gas and is pressurised to slightly above atmospheric pressure 1 bar and so takes on structural loads in order to maintain its shape. Venting or filling one or more smaller air filled ballonets (not shown) within the envelope is used to help maintain the correct lifting gas pressure as the airship climbs and descends.
The proposed flame arrester layout is also shown in the above figure.
Maximum Payloads
Replacing helium as a lifting gas with hydrogen and the flame arrester will affect the maximum payload of a given airship design.
The figure below is for an aluminium alloy mesh flame arrester with cell sizes of around length 3m, width 3m and height 2m. The mesh can be strengthened with interwoven carbon fiber. A weight allowance is taken into account for assembly as is a reduced lifting gas volume due to air-filled ballonets which are most inflated at sea level.
One and two mesh layers per panel are included, each capable of quenching a flame front in theory. However, two mesh layers provide a more robust design in terms of flame quenching (if there are occasional mesh weave imperfections) and prevention of re-ignition (more material to absorb post combustion heat within a cell).
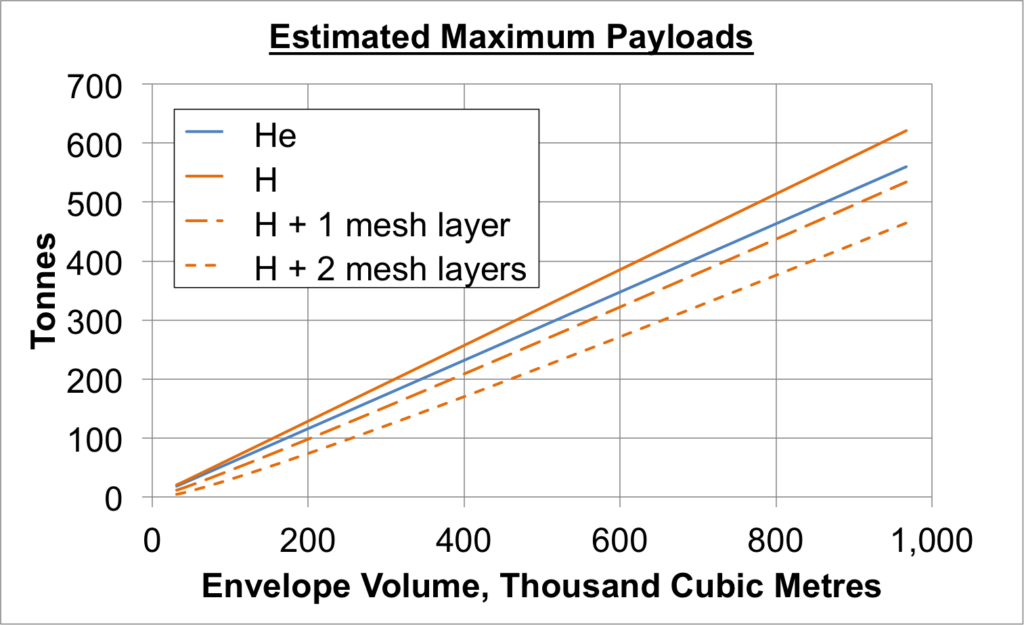
As research progresses, one aim is to progress to a robust one layer mesh design, the lighter option. Another aim is to use larger cell sizes. For example, doubling each cell dimension to length 6m, width 6m and height 4m will use the same weight of mesh and so the same payload results would apply (for the one and two layer mesh designs) but with a 4m thick combustion resistant region instead of 2m.
Certain design issues need to be investigated further including ignition caused by static within the envelope and embrittlement caused by hydrogen. However, the initial research will focus on the fundamental flame quenching properties of thin mesh designs for combustion of worst case (stoichiometric) hydrogen-air mixtures.
Note that perfectly mixed stoichiometric hydrogen-air throughout a cell is very unlikely. So the overall heat generated within a cell should be significantly less than the theory. This means there should be some flexibility in addressing higher heat concentrations within a cell.
Material Costs
At this initial research stage, we can refer to costs of materials (helium, hydrogen and mesh) rather than panel fabrication and assembly/installation (see figure below). The combined cost of hydrogen and mesh material is less than the helium cost.
That said, we would expect the initial cost of the hydrogen and completed flame arrester to exceed that of helium only. Over the life time of the airship, some of the cost difference will be recovered as the envelope is topped up with cheaper hydrogen instead of helium.
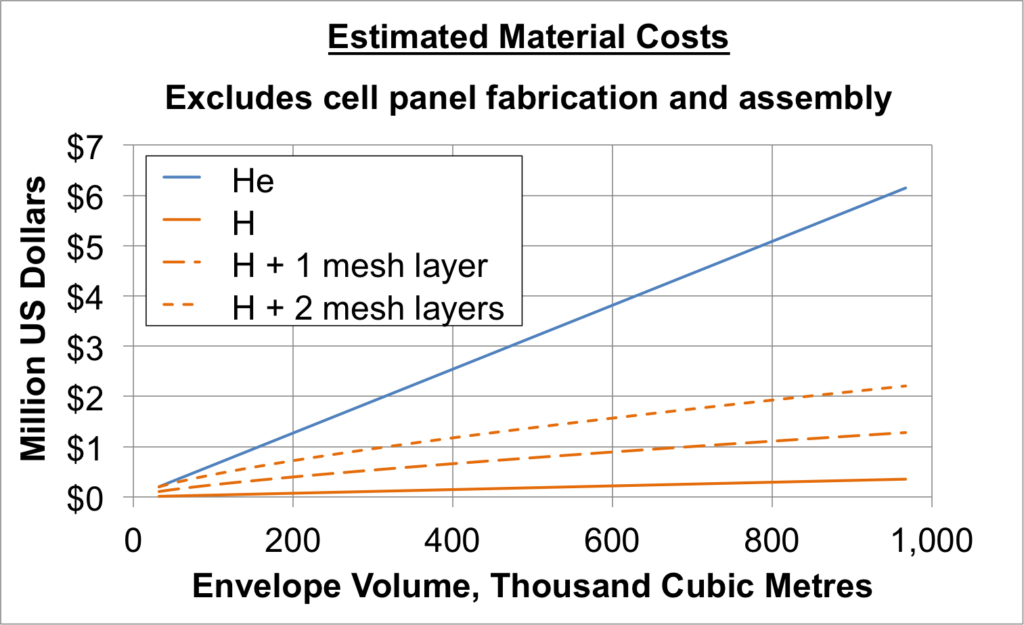
As reference, the following costs were used to produce the above figure:
Helium (Grade A) 7.946 US Dollars per cubic metre;
Hydrogen 0.457 US Dollars per cubic metre (from renewables);
Aluminium alloy mesh 6.050 US Dollars per square metre.